APQP (Расширенное планирование качества продукции), пример
APQP (Расширенное планирование качества продукции), В переводе с испанского «Расширенное планирование качества продукции» он представляет собой набор процедур и методов, используемых для разработки продуктов в отрасли, особенно в автомобильной..
Сложные продукты и цепочки поставок представляют много возможностей отказа, особенно когда запускаются новые продукты. APQP - это структурированный процесс проектирования продуктов и процессов, нацеленный на обеспечение удовлетворенности клиентов новыми продуктами или процессами..
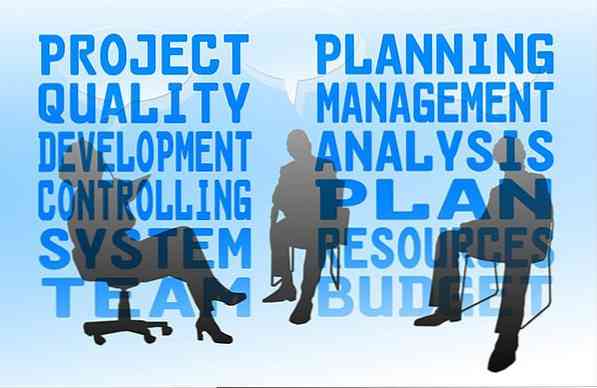
Этот подход использует инструменты и методы для снижения рисков, связанных с изменениями в новом продукте или процессе..
Его цель заключается в разработке стандартизированного плана требований к качеству продукции, который позволяет поставщикам разрабатывать продукт или услугу, которые удовлетворяют потребителя, облегчая общение и сотрудничество между различными видами деятельности..
В процессе APQP используется многофункциональная команда, которая занимается маркетингом, дизайном продукции, закупками, производством и распространением. Этот процесс используется General Motors, Ford, Chrysler и его поставщиками для своей системы разработки продукции..
индекс
- 1 Фазы
- 1.1 Этап 1: планирование и определение программы
- 1.2 Фаза 2: Дизайн и разработка продукта
- 1.3 Фаза 3: Проектирование и разработка процесса производства продукции
- 1.4 Этап 4: процесс и проверка продукта
- 1.5 Фаза 5: запуск, оценки и постоянное улучшение
- 2 Пример
- 2.1 Где включить APQP
- 2.2 Отрасли, которые его используют
- 3 Ссылки
фазы
APQP служит руководством в процессе разработки, а также стандартным способом обмена результатами между поставщиками и автомобильными компаниями. Он состоит из пяти этапов:
Этап 1: планирование и определение программы
Когда требование клиентов требует введения нового продукта или пересмотра существующего, планирование становится центральной темой, даже до обсуждения дизайна или изменения дизайна продукта..
На этом этапе планирование стремится понять потребности клиента, а также ожидания продукта.
Планирование включает в себя сбор необходимых данных для определения того, что хочет клиент, а затем использование этой информации для обсуждения характеристик продукта..
Затем вы можете определить программу качества, необходимую для создания продукта, как указано.
Результат этой работы включает в себя дизайн продукта, надежность и цели качества.
Этап 2: Дизайн и разработка продукта
Целью этого этапа является завершение дизайна продукта. Это также, где оценка жизнеспособности продукта вступает в игру. Результаты работы на этом этапе включают в себя:
- Проверка и проверка выполненного проекта.
- Определены спецификации материалов и требований к оборудованию.
- Анализ эффекта и режима отказа завершенного проекта для оценки вероятности отказа.
- Планы контроля созданы для создания прототипа продукта.
Этап 3: Проектирование и разработка процесса производства продукции
Этот этап фокусируется на планировании производственного процесса, который будет производить новый или улучшенный продукт.
Цель состоит в том, чтобы спроектировать и разработать производственный процесс с учетом технических характеристик и качества продукта, а также производственных затрат..
Процесс должен быть способен производить количества, необходимые для удовлетворения ожидаемого спроса потребителей, при сохранении эффективности. Результаты на этом этапе включают в себя:
- Полная конфигурация технологического процесса.
- Анализ влияния и режима отказа всего процесса для выявления и управления рисками.
- Качественные характеристики рабочего процесса.
- Требования к упаковке и отделке продукта.
Этап 4: процесс и проверка продукта
Это этап тестирования для проверки производственного процесса и конечного продукта. Шаги на этом этапе включают в себя:
- Подтверждение мощности и надежности производственного процесса. Аналогичным образом, из критерия приемлемости качества продукта.
- Проведение опытных производств..
- Тестирование продукта, чтобы подтвердить эффективность производственного подхода.
- Сделайте необходимые корректировки, прежде чем переходить к следующему этапу.
Этап 5: запуск, оценка и постоянное улучшение
На этом этапе запускается крупномасштабное производство с упором на оценку и улучшение процессов.
Основными элементами этого этапа являются уменьшение изменений процесса, выявление проблем, а также принятие корректирующих действий для поддержки постоянного улучшения.
Существует также сбор и оценка отзывов клиентов и данных, связанных с эффективностью процесса и планированием качества. Результаты включают в себя:
- Улучшение производственного процесса за счет уменьшения вариаций процесса.
- Улучшение качества доставки товара и услуг клиенту.
- Улучшение удовлетворенности клиентов.
пример
Где включить APQP
- Разработка требований от голоса клиента, используя реализацию функции качества.
- Разработка плана качества продукции, интегрированного в график проекта.
- Действия по разработке продукта, в которых перед выпуском дизайна передаются специальные характеристики или ключи к процессу разработки процесса. Это включает в себя новые формы и детали, более жесткие допуски и новые материалы.
- Разработка планов испытаний.
- Использование формальной проверки дизайна для отслеживания прогресса.
- Планирование, приобретение и установка соответствующего оборудования и инструментов процесса в соответствии с проектными допусками, указанными источником дизайна продукта.
- Сообщение предложений от сборочного и производственного персонала о том, как лучше собрать изделие.
- Установление адекватного контроля качества для специальных характеристик или ключей продукта или параметров процесса, которые все еще подвергаются риску потенциальных отказов.
- Проведение исследований стабильности и способности специальных характеристик, чтобы понять текущую вариацию и, таким образом, прогнозировать будущие характеристики с помощью статистического контроля процессов и возможностей процесса..
Отрасли, которые его используют
Компания Ford Motor опубликовала первое руководство по усовершенствованному планированию качества для своих поставщиков в начале 1980-х годов, что помогло поставщикам Ford разработать надлежащие средства контроля для предотвращения и обнаружения новых продуктов, тем самым поддерживая корпоративные усилия по обеспечению качества..
В конце 80-х годов основные производители автомобильной промышленности использовали программы APQP. Дженерал Моторс, Форд и Крайслер внедрили его и увидели необходимость объединиться, чтобы создать для своих поставщиков общее ядро принципов планирования качества продукции..
Руководящие принципы были разработаны в начале 1990-х годов для обеспечения соблюдения протоколов APQP в стандартизированном формате..
Представители трех производителей автомобилей и Американского общества по контролю качества создали группу требований к качеству, чтобы иметь общее понимание по темам, представляющим взаимный интерес для автомобильной промышленности..
Эта методология в настоящее время также используется прогрессивными компаниями, чтобы гарантировать качество и производительность посредством планирования.
ссылки
- Википедия, свободная энциклопедия (2018). Расширенное планирование качества продукции. Взято из: en.wikipedia.org.
- NPD Solutions (2018). Расширенное планирование качества продукции. Взято из: npd-solutions.com.
- Quality-One (2018). Расширенное планирование качества продукции (APQP). Взято с: quality-one.com.
- Приманки (2018). 5 этапов APQP: обзор основных требований. Взято с: cebos.com.
- Дэвид Ингрэм (2018). Расширенное планирование качества продукции. Малый бизнес - Chron.com. Взято с сайта: smallbusiness.chron.com.